3 outils statistiques sont des amis inséparables : le R et R, la Capabilité, et le SPC (ou Contrôle Statistique de Processus). Ces trois compagnons se retrouvent régulièrement pour échanger dans des lieux conviviaux comme les cafés Excel, Minitab ou autre, et bien que leurs noms puissent paraître intimidants, ils sont essentiels pour garantir des mesures et des processus fiables. Mais attention, pour en tirer le meilleur, il faut bien les connaître !
Premier ami à rencontrer : le R et R, l’ami de la fiabilité
Notre premier ami, le R&R (ou Etude de Répétabilité et Reproductibilité), est souvent un peu rude au premier abord avec son nom de barbare ! Pourtant, c’est un allié essentiel, car il nous aide à déterminer si notre système de mesure est à la fois fiable et précis. Le R&R est en fait composé de deux parties : l’EV (Erreur de Variation) et l’AV (Erreur de Reproductibilité).
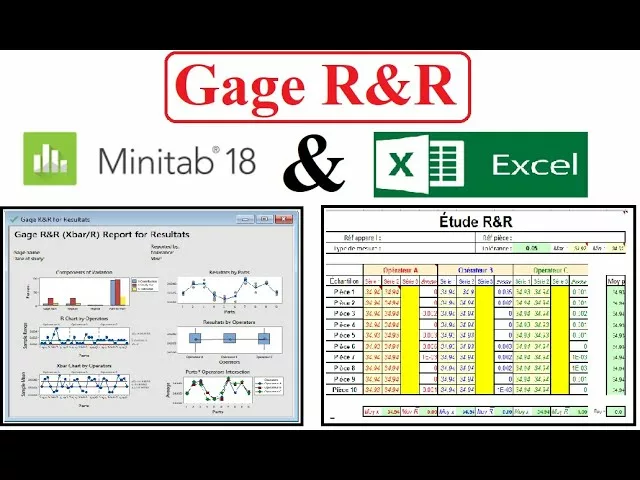
- L’EV (Erreur de Variation) : Elle montre la capacité d’un opérateur à obtenir les mêmes mesures en répétant plusieurs fois la même opération. Si l’EV est trop élevée, cela signifie que même en répétant la mesure, les résultats varient trop, ce qui remet en question la fiabilité de l’outil de mesure.
- L’AV (Erreur de Reproductibilité) : Elle représente la variation entre différents opérateurs qui mesurent le même objet. Une AV élevée signifie que la mesure dépend beaucoup de qui la réalise, ce qui n’est pas souhaitable.
- Le dg (ou erreur systémique, qui correspond au décalage entre la moyenne des mesures et la valeur de référence permet de connaitre le %R&R et le %PM.
Pour les calculer, c’est très simple, et pas forcément long:
– La méthode MSA (measurement system analysis), imposée dansl’automobile. Prendre 5 à 10 pièces, les mesurer 3 fois chacune par un opérateur, puis un second, puis un troisième. Les variations de mesure permettent de calculer un écart type pour un même opérateur, puis un écart type entre opérateurs. L’écart typ doit être significativement plus faible que la tolérance au plan.
– La capabilité de mesure, préférée pour les mesures réalisées par une seule machine de mesure. Mesurer 30 fois une même pièce et calculer la capa (voir l’amie suivante).
Le degré de précision ou % R&R permet de quantifier la fiabilité globale du système de mesure. En général, si le R&R est inférieur à 10 %, on peut considérer la mesure fiable. Entre 10 % et 30 %, la mesure est acceptable mais à surveiller ; au-delà de 30 %, il est préférable de revoir le processus de mesure.
Capabilité : l’Amie de la normalité
Une fois que les mesures sont fiables grâce à notre ami R&R, nous faisons appel à Capabilité, l’amie qui nous aide à savoir si notre processus est capable de répondre aux spécifications. Elle aime les distributions normales et exige que les données suivent cette forme pour que les résultats soient vraiment exploitables.
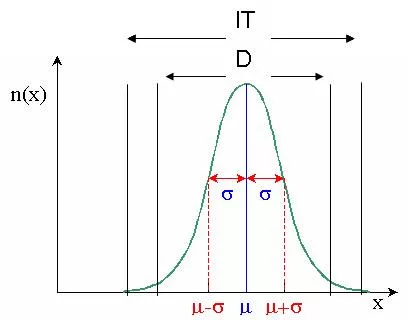
- La Normalité : La capabilité repose sur l’idée que les données doivent se répartir en cloche (ou distribution normale ou gaussienne) autour de la moyenne. Sans cela, les indices de capabilité ne reflètent pas fidèlement le comportement du processus.
- Les Indices de Capabilité : Ils sont les porte-parole de notre processus. Si le Cp et le Cpk, les principaux indices de capabilité, sont supérieurs à 1,33, on considère que le processus est capable. Un processus avec un Cp de 1,33 est généralement satisfaisant, mais pour des exigences plus strictes, un Cp de 1,67 ou même 2,00 est préférable.
Pour calculer les Cpk, c’est encore plus simple que pour le R&R. Internet vous l’expliquera mieux que moi
SPC : Le Stratège de la Conformité Continue
Avec des mesures fiables et un processus capable, notre troisième ami, le SPC, entre en scène pour jouer son rôle de stratège. Le SPC, ou Contrôle Statistique de Processus, aide l’ingénieur qualité à surveiller et contrôler la production à l’aide de cartes de contrôle. Ces cartes sont des outils puissants pour garantir la conformité des fabrications futures. Elle s’appuient sur des mesure de plusieurs pièces consécutives, dont on extrait la moyenne (X barre) et l’étendue (la différence maxi entre 2 mesures).
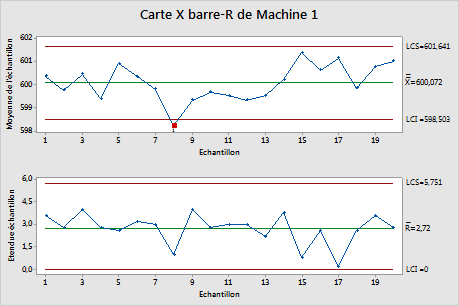
- Les Limites de Contrôle : Elles sont calculées à partir des données de capabilité, en général à ±3 fois l’écart-type par rapport à la moyenne du processus. Les limites de contrôle sont aussi important pour les moyennes que pour les étendues. Cela forme les limites supérieures et inférieures de contrôle, au sein desquelles les valeurs doivent rester.
- Les Règles du SPC : L’analyse des cartes de contrôle suit quelques règles simples. Par exemple, si une valeur dépasse les limites de contrôle, cela indique une anomalie. Mais même si toutes les valeurs sont bien dans les limites, si elles montrent des tendances inhabituelles (comme 7 points consécutifs en hausse), le SPC alerte l’ingénieur sur un possible dérèglement du processus.
Pour calculer les limites de contrôle, 2 méthodes aussi simples l’une que l’autre (une est plus rapide). MSA vous dira tout, mais Esquali vous l’expliquera et choisira l’option la plus adaptée à votre application.
En conclusion
Nos trois amis, le R&R, la Capabilité et le SPC, sont des compagnons fidèles de l’ingénieur qualité. Ils se soutiennent mutuellement et permettent, ensemble, d’obtenir des mesures précises, des processus capables, et des productions conformes. Un trio à ne pas négliger pour vous éviter tout produit non conforme, rebut, réclamation ou autre désagrément.
Esquali propose un module de formation ludique et rapide qui peut s’adapter à un public d’ingénieurs qualité, méthodes et production, à des techiciens et opérateurs de production ainsi qu’à des étudiants. N’hésitez pas à me contacter pour plus d’information.